Period: 6 months with potential extension and/or permanent hire.
Our client is a Danish international manufacturing company with facilities in several European countries.
The factory in Norway now needs a new Interim Plant Manager.
The right candidate with the right qualifications may be from Scandinavian.
Landscape and challenges
- Large strategic capex (100MDkk) in factory
- Responsibility for the manufacturing plant, and leading a team in a matrix organization
- History of turnover of some key positions
- Low performance track of the factory
- History of a misalignment of the organization to functional set up (Matrix), must be a culture change driver
- Challenge of turning around the factory and reinforcing the organization
Job Summary:
Highly skilled and experienced Interim Plant Manager to oversee the operations of the factory in Norway. The ideal candidate will ensure that manufacturing processes run reliably and efficiently, maintaining high standards of safety, quality, and productivity. Additionally, the candidate will play a key role in a large-scale automation project and lead a continuous improvement journey. The factory is part of a large manufacturing group based in Denmark; the Plant Manager will be an integral part of the operations management team.
Key Responsibilities:
- Operational Management: Plan, organize, direct, and run optimum day-to-day operations
- Production Oversight: Increase production capacity and flexibility while minimizing unnecessary costs and maintaining current quality standards.
- Efficiency Improvement: Develop and implement systems and processes that track and optimize productivity and standards, metrics, and performance targets.
- Safety and Compliance: Ensure all health and safety regulations are followed and maintain compliance with industry standards.
- Team Leadership: Share a trusting relationship, recruit, manage, and develop plant staff.
- Resource Allocation: Allocate resources effectively and fully utilize assets to produce optimal results.
- Data Analysis: Collect and analyze data to find places of waste or overtime and implement corrective actions as needed.
- Budget Management: Work with budgets, forecasting, and planning.
- Automation Project: Contribute to the planning and implementation of a large-scale project to automate the factory, ensuring seamless integration with existing processes.
- Continuous Improvement: Lead and drive continuous improvement initiatives to enhance operational efficiency, quality, and productivity.
Qualifications:
- Proven work experience as a Plant Manager in a manufacturing environment.
- Strong knowledge of business and management principles (budgeting, strategic planning, resource allocation, and human resources).
- Excellent leadership, decision-making, and people management skills.
- Ability to create accountability and lead by example.
- Strong team-building skills and a results-driven approach.
- Bachelor or master’s degree in engineering.
- Proficiency in Norwegian and English.
- Experience with continuous improvement methodologies.
Welcome with your application by registering your CV by using the button below as soon as possible, as the selection process is ongoing. If you have any questions about the assignment, please contact Håkan Ossmyr at hakan.ossmyr@mason.se or 0735 31 56 76.
Please note that we, unfortunately, cannot receive applications by mail.
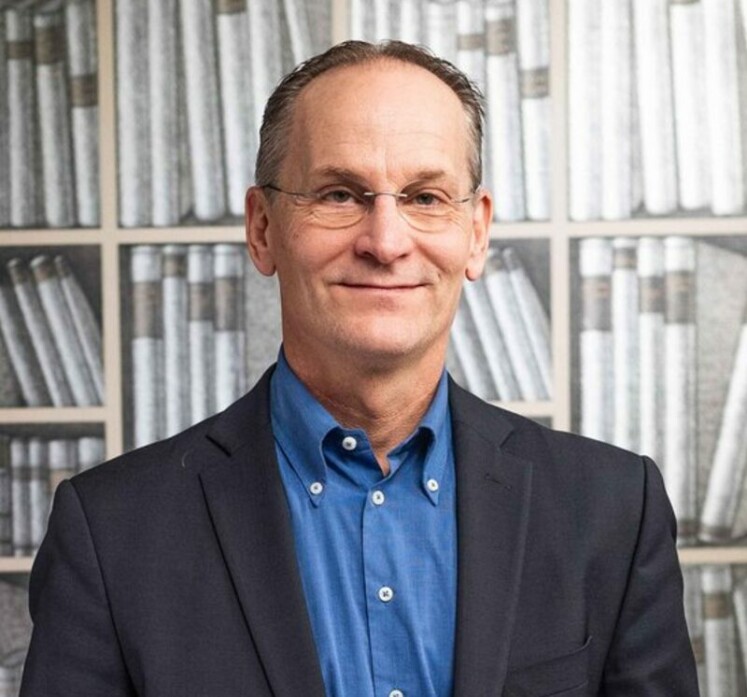